Une ère aux nouvelles dimensions
La chaîne, c’était hier. Aujourd’hui, la fabrication est individuelle et personnalisée grâce aux imprimantes 3D.
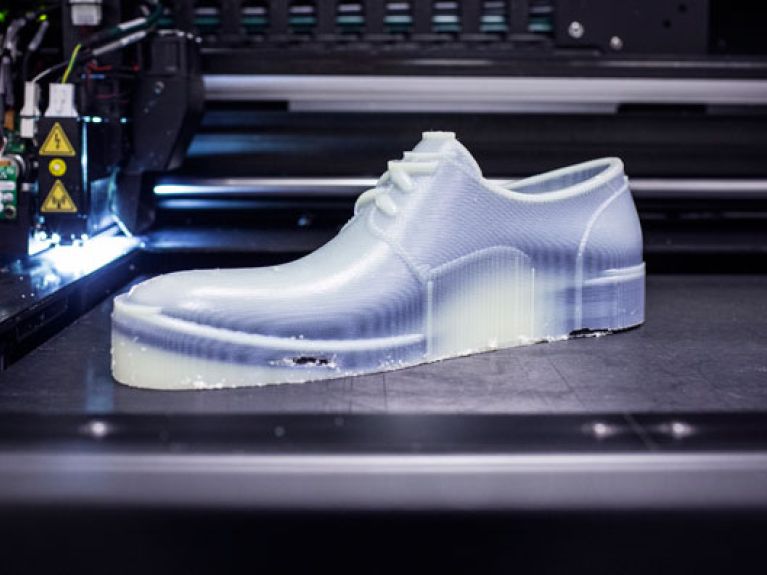
C’est une chaîne de vélo qui changea la vie d’Andy Middleton du jour au lendemain, le projetant littéralement dans une nouvelle dimension. Cette chaîne n’a pourtant rien de spectaculaire et n’entraînera jamais une bicyclette puisqu’elle est en plastique blanc. Andy Middleton se saisit de la chaîne et fait glisser chacun de ses maillons entre les doigts. Il semble hypnotisé par cet objet. Comme s’il ne pouvait pas encore croire à ce qu’il tient là, entre le pouce et l’index. Pour lui, cette pièce n’est pas une simple chaîne de vélo en plastique, c’est un petit miracle : elle a été fabriquée par une imprimante 3D.
Cela fait maintenant cinq ans qu’il tint cette chaîne de vélo pour la première fois entre les mains. À l’époque, on lui demanda s’il voulait entrer chez Objet, un fabricant israélien d’imprimantes 3D. On lui proposa de diriger les affaires de la société dans l’espace EPOA, c’est-à-dire en Europe, au Proche-Orient et en Afrique. Il n’avait jusque-là guère eu de contact avec la technologie de l’impression 3D, alors surtout connue des spécialistes. « Puis j’ai vu la chaîne de vélo sortie de l’imprimante 3D et j’ai su immédiatement que je voulais ce poste », se souvient le Britannique.
Aujourd’hui, il est assis sur un canapé en cuir noir dans son bureau inondé de lumière et vit dans un autre monde. Non seulement parce qu’il a quitté, avec sa femme et ses deux enfants, un Düsseldorf très chic pour s’installer près de Rheinmünster, où se trouve le site EPOA, dans ce qu’il appelle un Baden-Baden « tranquille ». Ou bien parce qu’il a aujourd’hui 100 collaborateurs et pas seulement un salarié, comme c’était le cas au début. Mais aussi parce que l‘entreprise qui l’a engagé en 2008 n’est plus ce qu’elle était il y a cinq ans.
Objet est devenu Stratasys. L‘entreprise israélienne qui, avec « Polyjet Matrix », a mis au point une technologie d’impression 3D pour des applications industrielles est devenue il y a un an un leader mondial israélo-américain qui s’intéresse maintenant à différents groupes-cibles. Il y a quelques mois, Stratasys a acquis la société MakerBot et s’adresse aussi aux particuliers qui veulent fabriquer chez eux la tasse qu’ils ont dessinée, leur propre étui de smartphone ou des jouets qui seront des pièces uniques.
C’est en effet possible avec une imprimante 3D. Et bien d’autres choses encore. Car la vraie raison pour laquelle le patron de l’espace EPOA vit dans un monde différent réside derrière cette technologie : un nombre croissant d’entreprises et de bricoleurs s’achètent une imprimante 3D. En 2012, les fabricants d’imprimantes 3D réalisèrent un chiffre d’affaires de 2,2 milliards de dollars dans le monde. D‘ici à 2015, estime le spécialiste américain Terry Wohlers, le chiffre d‘affaires devrait passer à 3,7 milliards de dollars. Selon Andy Middleton, l’Allemagne est l’un des marchés les plus importants. « Au total, l’industrie allemande possède déjà plus de 8500 imprimantes 3D et occupe ainsi la deuxième place derrière les États-Unis. »
On attribue à l’impression 3D des qualités presque magiques. « Elle met un terme à l’ère de la fabrication à la chaîne et sonne l’avènement d’une nouvelle époque », dit Middleton sur un ton laconique. Car cette technologie permet de fabriquer en masse des produits individualisés, en peu de temps et avec un faible investissement matériel et financier. Les imprimantes n’exhibent guère le niveau d’innovation élevé qu’elles représentent : elles ont la forme d’une caisse recouverte d’une peinture unie. Et elles ne sont pas toutes silencieuses. Une plaque transparente permet de voir ce qui se passe à l’intérieur. Lorsque l’impression d’une pièce est terminée, on ouvre le couvercle et le produit souhaité est là, présenté comme sur un plateau. L’une des technologies d’impression 3D est comparable à l’impression par jet d’encre : une tête d’impression munie de buses appose plusieurs couches d’un matériau liquide qui durcit ensuite à la lumière ultra-violette. Les entreprises fabriquent ainsi leurs prototypes, par exemple. Dont ces chaînes de vélo en plastique qui ont immédiatement convaincu Andy Middleton.
Ou les voitures miniatures dont les constructeurs automobiles ont besoin pour leurs démonstrations. L’impression 3D leur permet de faire des modifications sur place et à peu de frais, d’imprimer simultanément plusieurs versions et de décider en peu de temps quel modèle convient le mieux à une production en série. Ils peuvent ainsi vendre plus tôt et les investissements en matières premières et coûts de développement baissent énormément car on n’utilise que le matériau vraiment nécessaire. Les domaines d’application sont pratiquement illimités.
Le patron de l’espace EPOA passe la main sur ses cheveux poivre et sel soigneusement coiffés vers l’arrière et décline : on peut imprimer des chaussures pour Lady Gaga, des pièces de rechange pour les lave-linge, des pièces d’avion pour Boeing, mais aussi des produits alimentaires, des maisons, des dents, des os ou même des organes et des prothèses. Andy Middleton place d’ailleurs de grands espoirs dans la médecine. Il parle de chirurgiens qui réalisent la maquette d’une tumeur cérébrale pour s’exercer avant l’opération. « Les patients se réjouissent d’une plus grande probabilité de réussite de leur opération et les caisses d’assurance maladie de coûts en baisse », dit Middleton. Il est persuadé que les produits de masse seront bientôt remplacés par des produits individualisés et que la fabrication quittera les pays à bas salaires pour être relocalisée dans les pays industrialisés classiques.
Outre les produits personnalisés que l’impression 3D permet de fabriquer, la « prochaine révolution industrielle » porte sur un autre aspect : la production individualisée. Elle numérise le processus de fabrication et le rend ainsi plus souple, plus intelligent et, par-là, plus efficace. Cette deuxième tendance nous fait rêver. Avec par exemple des pièces qui semblent dirigées par une main invisible, sont placées sur des systèmes de transport se déplaçant en toute autonomie, et qui indiquent aux robots par un réseau sans fil comment elles doivent être travaillées. Mais, dans certaines de ses étapes, l‘industrie en est encore à la deuxième dimension. Cette double dimension s’exprime par exemple dans des piles de papier.
Johann Hofmann ne connaît que trop bien la « paperasserie » qui règne dans nombre d’entreprises. Il y a 26 ans, ce spécialiste de l’usinage fut presque déstabilisé par ces piles de papiers. Après des études de génie mécanique, il entra comme programmeur de machines aux ateliers de construction mécanique Maschinenfabrik Reinhausen (MR) à Ratisbonne, un leader mondial des combinateurs. Ses pièces permettent de maintenir une tension constante dans les réseaux de transport d’électricité des producteurs d’énergie. Passionné par la programmation, Hofmann se réjouissait à l’idée de passer ses journées à alimenter son ordinateur de codes chiffrés. Mais ses collègues à la fabrication déjouèrent ses plans ; il ne pouvait programmer en toute sérénité parce qu’ils l’interrompaient sans cesse.
Ce qui faisait le quotidien des usines dans les années 1980 est aujourd’hui impensable pour Hofmann. Les commandes qui arrivaient étaient toutes enregistrées sur papier, rangées dans des « chemises d’usi- nage » puis circulaient d’étape en étape. « Deux dames passaient leur journée à les distribuer aux opérateurs des machines, aux ajusteurs de l’outillage ou aux contremaîtres. » Lorsqu’une commande était modifiée, ce qui arrivait assez souvent, la chemise repartait chez les dames avec les modifications écrites à la main et celles-ci les apportaient à Hofmann. Celui-ci a de la patience mais il ne supportait plus ces interruptions permanentes. Il n’était qu’en début de carrière mais il savait que quelque chose devait changer s’il voulait se consacrer à sa passion.
Il est arrivé à son but, même s’il y a mis des décennies : Aujourd’hui, la Maschinenfabrik Reinhausen travaille en se basant totalement sur l’Internet, les feuilles de programmation et les chemises d’usinage ont disparu, la fabrication se fait sans « paperasserie ». Et ce n’est pas tout ce que Johann Hofmann a fait évoluer. Il a veillé à ce que tous les acteurs de la production, humains ou non-humains – c’est-à-dire l’entrepôt à outils, l’assurance de la qualité et les machines en plus des magasiniers et des contremaîtres – communiquent numériquement entre eux et s’informent en permanence sur l’état actuel de la fabrication. Tout cela fonctionne à l’aide d’une plaque tournante des données numériques appelée système cyber-physique.
Hofmann compare sa solution avec l’organisation d’un aéroport. « Imaginez que le pilote pose son avion et doive tout faire lui-même. Il s’informe pour savoir où il doit garer l’avion, demande à l’aiguilleur au sol de l’aider à manœuvrer jusqu’au parking et donne au personnel des instructions pour décharger les valises. À chaque fois, il doit remplir un formulaire. » Les processus à la MR ressemblaient à cela naguère. Et Hofmann d’ajouter, indigné : « au quotidien, le travail n’a guère évolué en la matière dans bien des entreprises allemandes ». Cela n’empêche pas de réussir, comme le montre la puissance de l’industrie allemande à l’exportation. Mais les attentes envers les entreprises de fabrication augmentent. Nicolas Maier-Scheubeck, le directeur de la MR et patron de Johann Hofmann, résume bien le problème : « chaque client obtiendra son produit sur mesure mais, à l’usine, les étapes de la production doivent être standardisées. »
Il a fallu 20 ans pour que cela fonctionne parfaitement. Johann Hofmann ne s’étonne plus quand on lui demande pourquoi sa solution a eu besoin de tant de temps. « Nous avons d’abord dû nous faire une idée approfondie de toutes les données à traiter et acquérir les connaissances correspondantes pour trouver ensuite un moyen de relier intelligemment tous les acteurs de la production. Un tel volume de données exige beaucoup de temps. » Il est fier que la solution qu’il a élaborée réponde aujourd’hui aux exigences d’une usine numérique. Et il constate en souriant : « c’est bien qu’on ait trouvé un mot pour cela avec le terme d’industrie 4.0 ».
Rayonnant, il parcourt le hall de fabrication en disant qu’il n’y a pour lui aujourd’hui rien de plus beau que d’écouter parler les machines. Pour savoir exactement ce qu’elles disent. Des décennies après son entrée dans cette entreprise familiale, il ne peut toujours pas programmer en paix. Ce n’est d’ailleurs plus son travail. Il arrive que des collègues surgissent dans son bureau parce qu’ils ont une suggestion à faire pour améliorer les choses. Aujourd’hui, il s’en réjouit car, la plupart du temps, il peut ainsi affiner sa solution et se rapprocher encore plus de son rêve, une mise en réseau totale de l’usine. ▪