Aufbruch in neue Dimensionen
Fließband war gestern. Heute wird individuell und personalisiert gefertigt: 3-D-Drucker machen es möglich.
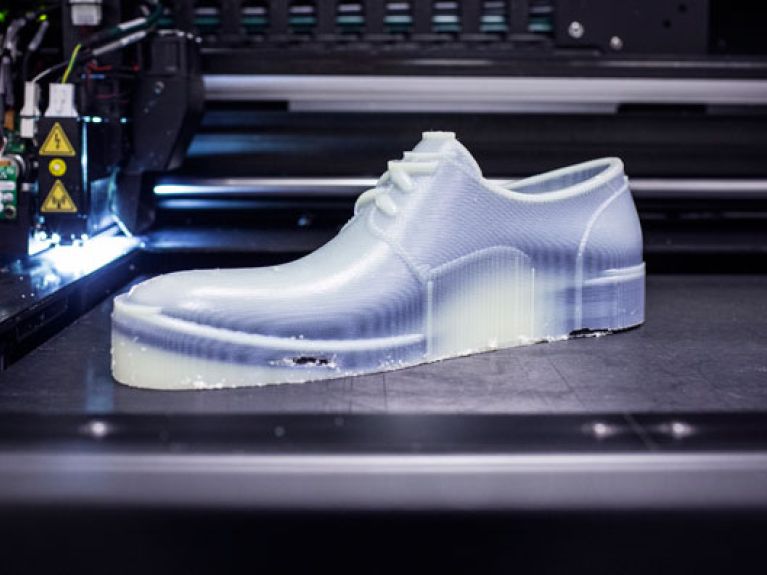
Eine Fahrradkette war es, die das Leben von Andy Middleton von heute auf morgen veränderte. Ihn buchstäblich in eine neue Dimension manövrierte. Dabei ist sie alles andere als spektakulär. Und sie wird auch nie ein echtes Fahrrad antreiben. Denn sie besteht aus weißem Plastik. Andy Middleton nimmt die Fahrradkette in die Hand und lässt jede einzelne Lasche durch seine Finger gleiten. Wie hypnotisiert blickt er das Plastikteil an. Als könne er immer noch nicht glauben, was er da zwischen Daumen und Zeigefinger hält. Für ihn ist das Teil nicht einfach eine Fahrradkette aus Plastik. Für ihn handelt es sich um ein kleines Wunder. Denn die Kette wurde von einem 3-D-Drucker gefertigt.
Gut fünf Jahre ist es jetzt her, dass er die Fahrradkette zum ersten Mal in der Hand hielt. Damals wurde er gefragt, ob er bei Objet einsteigen wolle, einem israelischen Hersteller von 3-D-Druckern. Man bot ihm an, von Deutschland aus das Geschäft im EMEA-Raum, also in Europa, im Nahen Osten und in Afrika zu verantworten. Mit der damals vor allem in Fachkreisen bekannten 3-D-Drucktechnologie hatte er bis zu diesem Zeitpunkt wenig zu tun gehabt. „Dann sah ich die Fahrradkette aus dem 3-D-Drucker und wusste sofort, dass ich den Job machen will“, erinnert sich der gebürtige Brite.
Jetzt sitzt er auf einer schwarzen Ledercouch in seinem lichtdurchfluteten Büro und lebt in einer anderen Welt. Nicht nur, weil er mit seiner Frau und den beiden Kindern vom schicken Düsseldorf in das, wie er selbst sagt, „gemütliche“ Baden-Baden nahe Rheinmünster gezogen ist, wo sich der EMEA-Standort befindet. Oder weil er heute 100 Mitarbeiter hat und nicht nur einen einzigen, wie am Anfang. Sondern auch, weil das Unternehmen, das ihn 2008 engagierte, nicht mehr ist, was es vor fünf Jahren war.
Aus Objet wurde Stratasys. Aus einem israelischen Unternehmen, das mit „Polyjet Matrix“ eine spezielle 3-D-Drucktechnologie für industrielle Anwendungen entwickelt hat, ist vor einem Jahr ein US-amerikanisch-israelischer Weltmarktführer geworden, der sich an diverse Zielgruppen wendet. Vor einigen Monaten erwarb Stratasys das Unternehmen MakerBot und spricht nun auch Privatkunden an, die zu Hause eine eigens kreierte Tasse, ihre individuelle Smartphone-Hülle oder einzigartige Spielzeugfiguren herstellen können.
Das ist mit 3-D-Druckern möglich. Und noch viel mehr. Denn der wahre Grund, warum der EMEA-Chef in einer veränderten Welt lebt, verbirgt sich hinter der 3-D-Drucktechnologie. Immer mehr Firmen und Hobbytüftler kaufen sich einen 3-D-Drucker. 2012 erwirtschafteten die 3-D-Druckerhersteller global 2,2 Milliarden Dollar. Bis 2015, hat der US-Branchenexperte Terry Wohlers prophezeit, soll der Umsatz auf 3,7 Milliarden Dollar wachsen. Deutschland ist laut Andy Middleton einer der wichtigsten Märkte. „Insgesamt verfügt die deutsche Industrie bereits über 8500 3-D-Drucker. Sie belegt damit weltweit den zweiten Platz hinter den USA.“
Es sind nahezu magische Fähigkeiten, die dem 3-D-Druck nachgesagt werden. „Er beendet das Zeitalter der Fließbandproduktion und leitet eine neue Epoche ein“, sagt Middleton lakonisch. Denn mit der Technologie lassen sich massenhaft individualisierte Produkte herstellen – in kurzer Zeit und mit geringem materiellem und finanziellem Aufwand. Ihren hohen Innovationsgrad sieht man den Druckern kaum an: Kastenförmig sind sie und einfarbig lackiert. Und nicht alle sind gerade leise. Was in ihrem Innersten vor sich geht, offenbart eine transparente Scheibe. Ist ein Teil fertig gedruckt, klappt man den Deckel auf – und wie auf dem Präsentierteller liegt dort das gewünschte Produkt. Eine der 3-D-Drucktechnologien ist mit dem Tintenstrahldruck vergleichbar: Ein zunächst flüssiges Material wird durch einen Druckkopf, der mehrere Düsen hat, schichtweise aufgetragen und härtet anschließend unter UV-Licht aus. Unternehmen stellen auf diese Weise zum Beispiel Prototypen her. Jene Fahrradketten aus Plastik etwa, die Andy Middleton sofort überzeugten.
Oder Miniaturautos, die Autohersteller zu Demonstrationszwecken benötigen. Der 3-D-Druck erlaubt es ihnen, schnell, günstig, ohne großen Aufwand sowie an Ort und Stelle Änderungen vorzunehmen, unterschiedliche Versionen gleichzeitig auszudrucken und in kurzer Zeit zu entscheiden, welches Modell sich am besten für die Serie eignet. Sie generieren früher Umsätze und auch der Rohstoff- und Fertigungsaufwand sinkt enorm, weil nur so viel Material verwendet werden muss, wie tatsächlich benötigt wird. Die Einsatzgebiete sind nahezu grenzenlos.
Der EMEA-Chef fährt sich durch die streng nach hinten gekämmten, grau melierten Haare und beginnt aufzuzählen: Schuhe für Lady Gaga, Ersatzteile für die Waschmaschine, Flugzeugteile für Boeing, aber auch Lebensmittel, Häuser, Zähne, Knochen oder sogar Organe und Prothesen kann man ausdrucken. Überhaupt setzt Andy Middleton große Erwartungen in die Medizin. Er erzählt von Chirurgen, die Modelle von einem Hirntumor anfertigen, um vor der Operation daran zu üben. „Patienten freuen sich über eine hohe Erfolgswahrscheinlichkeit, Krankenkassen über sinkende Kosten“, so Middleton. Er geht fest davon aus, dass Massenprodukte bald von massenhaft erzeugten individualisierten Produkten abgelöst werden und die Produktion aus Niedriglohnländern zurück in die klassischen Industrieländer wandert.
Neben diesen personalisierten Produkten, wie der 3-D-Druck sie ermöglicht, geht es bei der „nächsten industriellen Revolution“ um einen weiteren Punkt: die individualisierte Produktion. Sie digitalisiert den Fertigungsprozess und macht ihn so flexibel, intelligent und damit effizient. Dieser zweite Trend lädt zu den kühnsten Träumereien ein. Von Werkstücken etwa, die wie von Geisterhand gesteuert auf autonom fahrende Transportsysteme gepackt werden und über ein Drahtlosnetzwerk mitteilen, wie hoch ihr Bearbeitungsbedarf ist. Noch ist die Industrie in einigen ihrer Abläufe aber in der zweiten Dimension verhaftet. Einen Ausdruck findet die Zweidimensionalität zum Beispiel in Papierstapeln.
Johann Hofmann kennt diese „Zettelwirtschaft“ vieler Unternehmen nur zu gut. Vor 26 Jahren verlor der Fertigungsspezialist vor lauter Papierstapeln beinahe die Orientierung. Nach seinem Maschinenbaustudium stieg er als Maschinenprogrammierer bei der Maschinenfabrik Reinhausen (MR) in Regensburg ein, einem Weltmarktführer für Stufenschalter. Die Produkte sorgen dafür, dass in den Stromübertragungsnetzen der Energieversorger immer eine konstante Spannung herrscht. Als leidenschaftlicher Programmierer hatte sich Hofmann darauf gefreut, den ganzen Tag nichts anderes zu tun, als seinen Computer mit Zahlencodes zu füttern. Doch die Kollegen aus der Fertigung durchkreuzten seinen Plan. Er konnte nicht in Ruhe programmieren, weil sie ihn ständig unterbrachen.
Was in den achtziger Jahren Fabrikalltag war, ist für Johann Hofmann heute unvorstellbar: Eingehende Aufträge wurden ausnahmslos auf Papier festgehalten, in sogenannten Werkermappen verstaut und dann von Station zu Station weitergereicht. „Es gab zwei Damen, die den ganzen Tag mit nichts anderem beschäftigt waren, als die Mappen an die Maschinenbediener, Werkzeugeinsteller oder Meister auszugeben.“ Änderte sich etwas am Fertigungsauftrag – was nicht selten vorkam –, ging die Mappe mit den handschriftlichen Änderungen an die Damen zurück, die sie wiederum an Hofmann weiterreichten. Zwar ist der Oberpfälzer ein geduldiger Mensch, aber die ständigen Unterbrechungen hielt er kaum aus. Dabei stand er erst am Anfang seines Berufslebens. Er wusste: Um seinem Job mit Leidenschaft nachgehen zu können, musste sich etwas ändern.
Dieses Ziel hat er erreicht, auch wenn bis dahin einige Jahrzehnte vergingen. Heute wird in der Maschinenfabrik Reinhausen komplett webbasiert gefertigt. Sprich: Programmierblätter und Werkermappen gehören der Vergangenheit an – die Fertigung arbeitet papierlos. Und das ist noch lange nicht alles, was Johann Hofmann verändert hat. Er hat auch dafür gesorgt, dass alle am Produktionsprozess beteiligten menschlichen und nicht-menschlichen Akteure – also neben den Lageristen und den Meistern etwa das Werkzeuglager, die Qualitätssicherung oder die Fertigungsmaschinen – digital miteinander kommunizieren und sich ständig über den aktuellen Stand informieren. Das alles funktioniert mithilfe einer digitalen Datendrehscheibe, einem sogenannten cyberphysischen System.
Seine Lösung vergleicht Hofmann mit der Organisation eines Flughafens. „Stellen Sie sich vor, der Pilot landet seine Maschine und muss alles selbst machen. Er informiert sich darüber, wo er parken kann, bittet den Bodenlotsen, ihn in den Parkplatz zu manövrieren, und gibt dem Bodenpersonal Anweisungen für das Ausladen der Koffer. Und er muss für all das ein Formular ausfüllen.“ So ähnlich gestalteten sich früher die Abläufe in der MR. Hofmann ergänzt empört: „Und in vielen deutschen Fabriken sieht so noch heute der Arbeitsalltag aus.“ Zwar lässt es sich so erfolgreich arbeiten, das zeigt nicht nur die Exportstärke der deutschen Industrie. Aber die Anforderungen an produzierende Unternehmen steigen. Nicolas Maier-Scheubeck, MR-Geschäftsführer und Vorgesetzter von Johann Hofmann, bringt das Problem auf den Punkt: „Jeder Kunde bekommt sein kariertes Maiglöckchen, aber fabrikintern muss der Produktionsprozess standardisiert ablaufen.“
20 Jahre hat es gedauert, bis das reibungslos funktioniert hat. Über die Frage, warum er für seine Lösung so lange gebraucht habe, wundert sich Johann Hofmann schon lange nicht mehr. „Wir mussten uns zunächst einen Überblick über die Daten und das damit verbundene Wissen verschaffen, um dann einen Weg zu finden, alles intelligent zu verknüpfen. Bei den riesigen Datenmengen dauert das etwas.“ Dass seine Lösung heute die wesentlichen Anforderungen einer digitalen Fabrik erfüllt, macht ihn stolz. Schmunzelnd stellt er fest: „Schön, dass mit ‚Industrie 4.0‘ nun auch ein Name gefunden wurde.“
Mit strahlenden Augen geht er durch die Fertigungshalle und erzählt, dass es heute nichts Schöneres für ihn gebe, als den Maschinen beim Sprechen zuzuhören. Und genau zu wissen, worüber sie reden. In Ruhe programmieren kann er auch Jahrzehnte nach seinem Einstieg in das familiengeführte Unternehmen nicht. Aber das ist auch nicht mehr seine Aufgabe. Es kommt zwar immer noch vor, dass Kollegen in sein Büro platzen, weil sie einen Verbesserungsvorschlag haben. Heute freut er sich darüber – denn meistens kann er die Lösung weiter verbessern und kommt seinem Traum von der totalen Vernetzung ein Stück näher. ▪