Viaje hacia una nueva dimensión
La línea de montaje pertenece al pasado. Hoy se produce en forma personalizada: con impresoras 3D
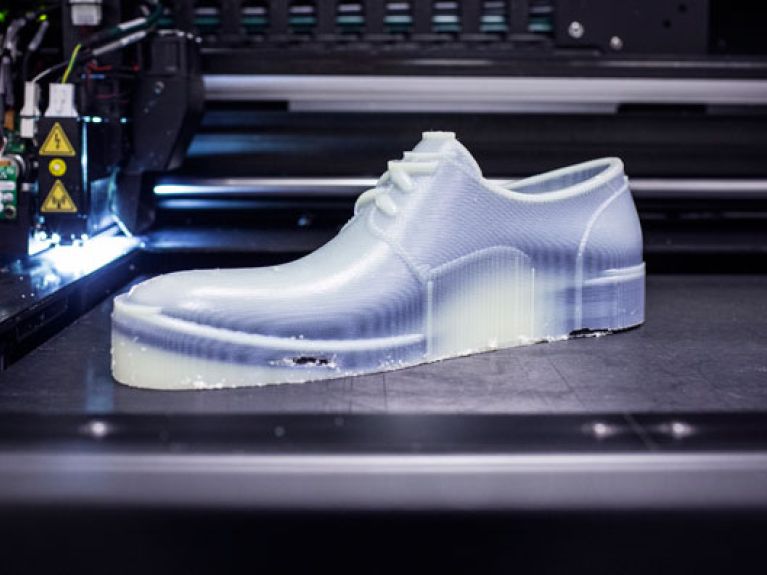
Una cadena de bicicleta fue lo que cambió la vida de Andy Middleton de un día para otro… y lo catapultó literalmente hacia una nueva dimensión. La cadena no es espectacular, ni nunca será usada en una bicicleta real, ya que es de plástico blanco. Andy Middleton toma la cadena en una mano y deja deslizarse cada uno de los eslabones por sus dedos. Como hipnotizado la mira una y otra vez. Como si no pudiera creer qué tiene entre el pulgar y el índice. Para Middleton, no es solo una cadena de plástico para bicicleta, sino todo un milagro, pues fue producida con una impresora 3D.
Hace ya más de cinco años que tuvo la cadena para bicicleta por primera vez en sus manos. Entonces se le preguntó si quería trabajar para Objet, un fabricante israelí de impresoras 3D. Se le ofreció coordinar desde Alemania los negocios de la empresa en el área EMEA, es decir, Europa, el Oriente Próximo y África. Hasta entonces había tenido poco contacto con la tecnología de impresión 3D, conocida sobre todo en círculos de especialistas. “Entonces vi la cadena de bicicleta hecha con la impresora 3D y de inmediato supe que quería hacer el trabajo”, recuerda Middleton, nacido en Gran Bretaña. Ahora se halla sentado en un sofá de cuero negro en una oficina bañada de luz y vive en otro mundo. No solo porque se mudó con su esposa y los dos hijos de la elegante Düsseldorf a Rheinmünster, cerca de Baden-Baden, donde tiene su sede EMEA. Y porque hoy tiene 100 empleados y no solo uno, como al comienzo, sino también porque la empresa que lo contrató tampoco es ya lo que era hace cinco años.
Objet se llama hoy Stratasys. La empresa israelí que desarrolló “Polyjet Matrix”, una tecnología especial de impresión 3D para aplicaciones industriales, se transformó hace un año en una empresa líder mundial estadounidense-israelí que con sus productos se dirige a diversos grupos destinatarios. Hace algunos meses, Stratasys compró la empresa MakerBot y ofrece soluciones ahora también para clientes particulares, que quieran crear en su casa una taza de diseño propio, su funda individual para smartphone o singulares figuras de juguete.
Ello es posible con impresoras 3D. Y mucho más. Ya que la verdadera razón por la que el director de EMEA vive en otro mundo es la tecnología de impresión 3D. Cada vez más empresas y particulares compran una impresora 3D. En 2012, los fabricantes de impresoras 3D facturaron en todo el mundo 2200 millones de dólares. El experto en impresión 3D Terry Wohlers estima que la facturación aumentará hasta 2015 a 3700 millones de dólares por año. Según Middleton, Alemania es uno de los mercados más importantes. “La industria alemana dispone en total de más de 8500 impresoras 3D, ocupando el segundo lugar después de Estados Unidos”, agrega.
La impresión 3D parece tener cualidades mágicas. “Termina con la era de la producción uniforme en serie y da comienzo a una nueva época”, dice Middleton lacónicamente. Con la tecnología pueden producirse en masa productos individualizados, rápidamente, con poco material y a bajo costo. A las impresoras no se les nota a primera vista su potencial innovador: tienen forma de cajón, son de un solo color y generalmente muy ruidosas. Lo que sucede en su interior puede verse a través de una ventanilla. Cuando finaliza la impresión de una pieza, se abre la tapa y el producto deseado se halla terminado sobre una bandeja. Una de las tecnologías de impresión 3D es comparable a la de tinta: un material líquido es aplicado capa sobre capa a través de una boquilla y endurecido con luz ultravioleta. Empresas producen así prototipos, por ejemplo las cadenas de plástico para bicicleta que convencieron de inmediato a Andy Middleton.
O autos en miniatura, que los fabricantes de vehículos necesitan para fines demostrativos. La impresora 3D les permite realizar cambios de inmediato, rápidamente, a bajo costo y sin mucho trabajo y decidir en poco tiempo qué modelo se adecua más para ser fabricado en serie. Así se generan ventas tempranamente y también el consumo de material se reduce enormemente, porque se utiliza tanto material como realmente se necesita. Las posibilidades son prácticamente ilimitadas.
El director de EMEA se pasa la mano por los cabellos y comienza a enumerar: zapatos para Lady Gaga, repuestos para lavarropas, partes de avión para Boeing, alimentos, casas, dientes, huesos y hasta órganos y prótesis. Andy Middleton deposita grandes esperanzas particularmente en la medicina. Nos cuenta de cirujanos que encargan el modelo de un tumor cerebral para practicar con él antes de la operación. “Los pacientes se alegran de que las posibilidades de éxito aumenten y las cajas de seguro médico, por los menores costos”, dice Middleton, que está convencido de que la producción en masa será sustituida pronto por una gran cantidad de productos individualizados y de que la producción que hoy se lleva a cabo en países de bajos sueldos regresará a los países industrializados clásicos.
Además de esos productos personalizados posible gracias a la impresión 3D, esencial en la “próxima revolución industrial” es otro punto: la individualización. La impresión 3D digitaliza el proceso de producción, haciéndolo flexible, inteligente y eficiente. Ello da alas a la fantasía y permite soñar con piezas que, comandadas como por una mano invisible, son cargadas sobre sistemas de transporte que se mueven autónomamente y pueden comunicar a través de una red inalámbrica qué necesitan aún para ser completadas. Algunos procesos industriales, sin embargo, se halla aprisionados en dos dimensiones. Una expresión de ello son, por ejemplo, las montañas de papel.
Johann Hofmann conoce bien ese “método de los papelitos” practicado en muchas empresas. Hace 26 años, este especialista en producción perdió por ello casi la orientación. Luego de sus estudios de fabricación de maquinaria comenzó a trabajar como programador de máquinas en la fábrica Maschinenfabrik Reinhausen (MR), en Ratisbona, líder mundial en cambiadores de tomas. Sus dispositivos aseguran que en las redes de distribución de energía el voltaje se mantenga constante. Hofmann, un apasionado programador, esperaba no hacer otra cosa todo el día que introducir códigos numéricos en su computadora. Los colegas de la producción, sin embargo, desbarataron su plan. No podía programar con tranquilidad, porque constantemente le preguntaban algo.
Lo que en los años 1980 era algo normal en las fábricas, es hoy completamente inimaginable para Johann Hofmann. Los encargos que entraban eran registrados sin excepción en papel, ordenados en carpetas de trabajo y pasados de estación a estación. “Había dos señoras que no hacían todo el día otra cosa que entregar las carpetas a los operadores de máquinas, ajustadores o maestros”, recuerda. Si algo cambiaba en el encargo –lo que sucedía bastante a menudo– la carpeta regresaba con las nuevas indicaciones escritas a mano a las señoras, que a su vez se la pasaba a Hofmann. Si bien este tiene paciencia, las constantes interrupciones lo sacaban de quicio, no obstante estar al comienzo de su carrera profesional. Hofmann llegó a la conclusión de que para que pudiera realizar con pasión su trabajo, algo debía cambiar.
Y lo logró, si bien debieron pasar varias décadas. Hoy, en la fábrica Maschinenfabrik Reinhausen se produce por completo sobre la base de un sistema de ejecución en red. Las hojas de los programadores y las carpetas de trabajo pertenecen al pasado. La producción se lleva a cabo sin papeles. Y eso no es todo lo que cambió Johann Hofmann. También logró que todos los actores en el proceso de producción, humanos y no humanos –es decir, los encargados de depósito y los maestros, también el almacén de herramientas, el aseguramiento de calidad y las máquinas mismas– se comuniquen entre sí en forma digital y se informen mutuamente sobre el estado de la producción. La base de ello es una plataforma digital central, un “sistema ciberfísico”.
Hofmann compara su solución con la organización de un aeropuerto: “Imagínese que el piloto aterrice y deba hacer todo solo. Se informa dónde puede aparcar, le pide al señalero que lo lleve allí y le da instrucciones al personal de tierra para descargar el equipaje. Y para todo ello debe rellenar sendos formularios.” Muy parecidos eran antes los procesos de trabajo en MR. “Y lo siguen siendo en muchas fábricas alemanas”, agrega Hofmann. Así también se puede trabajar exitosamente, como lo demuestran las cifras de exportación de la industria alemana. Las exigencias a la industria, sin embargo, aumentan. Nicolas Maier-Scheubeck, gerente de MR y jefe de Johann Hofmann, resume el punto en una frase: “Cada cliente recibe su producto individualizado, pero en la fábrica, el proceso de producción debe llevarse a cabo en forma estandarizada.”
Llevó 20 años perfeccionar el sistema. A la pregunta de por qué tanto tiempo, Johann Hofmann responde: “Primer debimos obtener un panorama de todos los datos y conocimientos y luego hallar un método para interconectarlos inteligentemente. Dada la gran cantidad de datos, ello lleva su tiempo”. Que su solución pueda llamarse hoy con razón “fábrica digital” lo llena de orgullo. Con una sonrisa agrega: “Y hoy hasta tiene un nombre: industria 4.0.”
Feliz se pasea hoy por las naves de producción y dice que no hay nada más hermoso que escuchar a las máquinas comunicarse entre sí. Y saber exactamente de qué están hablando. Programar tranquilo, sin embargo, tampoco puede diez años después de comenzar a trabajar en MR. Ni tampoco es hoy su trabajo. Si bien sucede que colegas entren a su oficina con una propuesta de mejora, hoy se alegra, ya que por lo general la solución perfecciona un poco más el sistema y lo aproxima algo más al sueño de la interconexión total en red. ▪