Entering new dimensions
The assembly line is passé. Today articles are personalized and manufactured individually thanks to 3D printers.
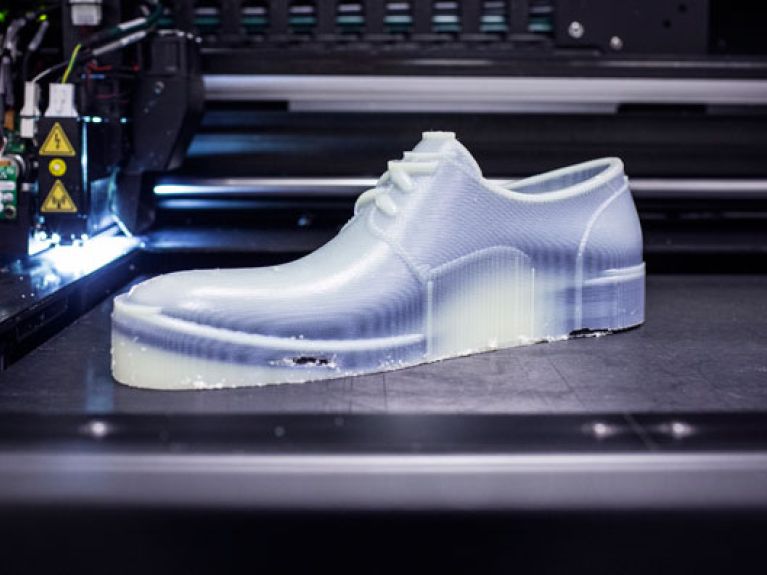
It was a bicycle chain that changed Andy Middleton’s life from one day to the next – and literally manoeuvred him into a new dimension. Yet it’s nothing spectacular. And it will never be used to drive a real bike, because it’s made of white plastic. Andy Middleton picks up the bicycle chain and lets every single link slip through his fingers. He looks at the plastic part as though hypnotized – as if he still can’t believe what he is holding between his thumb and forefinger. For him this part is not just a bicycle chain made of plastic. For him it’s a little miracle. After all, this chain was made by a 3D printer.
It’s over five years now since he held the bicycle chain in his hand for the first time. That was when he was asked to join Objet, an Israeli manufacturer of 3D printers. They offered him the job of running the business in the EMEA region (Europe, the Middle East and Africa) from Germany. Up to this point in time he had had little to do with 3D printing technology, which was then only really well known among experts. “When I saw the bicycle chain come out of the 3D printer I immediately knew I wanted to do the job,” UK-born Middleton recalls.
Now he sits on a black leather couch in his light-filled office and is living in a different world. Not only because he has moved with his wife and two children from trendy Dusseldorf to what he calls “cozy” Baden-Baden near Rheinmünster, where the EMEA central office is based. Nor because he now has 100 people working for him – and not just one like at the beginning. But also because the company that hired him in 2008 is no longer what it was five years ago.
Objet has become Stratasys. A year ago, the Israeli company that developed Polyjet Matrix – a special 3D printing technology for industrial applications – became a US- Israeli world market leader serving a wide range of different target groups. A few months ago Stratasys acquired MakerBot and now also targets private customers, who can use its products to make a self-designed cup, an individual smartphone case, or unique toy figures at home.
All of these things are possible with 3D printers. And a lot more – because the true reason why the EMEA boss lives in a changed world lies hidden behind the 3D printing technology. More and more companies and hobby inventors are buying 3D printers. In 2012 the 3D printer manufacturers generated a total turnover of 2.2 billion dollars worldwide. US industry expert Terry Wohlers predicts that sales will grow to 3.7 billion dollars by 2015. According to Andy Middleton, Germany is one of the most important markets. “German industry already has a total of 8,500 3D printers, putting it in second place in the world after the USA.”
3D printing is reputed to have almost magical abilities. “It’s ending the era of assembly-line production and ushering in a new epoch,” says Middleton laconically. This is because the technology makes it possible to mass-produce customized products – in a short time and at low cost in terms of materials and finance. When you look at the printers, it’s hard to imagine how highly innovative they are. They’re box-shaped and painted in a single colour. And all of them are not exactly quiet either. A transparent disc reveals what is going on inside. Once a part is finished, you lift the cover and there it is: the product you asked it to make! One of the 3D printing technologies is comparable to ink-jet printing: a liquid material is applied in layers by a print head with several nozzles; this material subsequently hardens under ultraviolet light. Companies use this method to make prototypes, for example – like those plastic bicycle chains that immediately convinced Andy Middleton.
Or the technology can be used to produce the kind of miniature cars that car makers need for demonstration purposes. 3D printing allows them to make changes quickly, cheaply, on the spot and without a lot of effort. They can have different versions printed simultaneously and quickly decide which model is best suited for the respective series. 3D printers start generating revenues earlier; they also greatly simplify production processes and reduce the amount of raw materials required, because you only use as much as you actually need. The areas of application are virtually limitless.
The EMEA boss runs his fingers through his severely combed-back greying hair and starts listing them: shoes for Lady Gaga, spare parts for washing machines, aircraft parts for Boeing – but also foodstuffs, houses, teeth, bones and even organs and prostheses can all be printed. Andy Middleton has great expectations in the medical field in particular. He talks about surgeons who make models of brain tumours to practise on before an operation. “Patients like the fact that this improves the prospects of success, and health insurance companies like the cost savings,” says Middleton. He firmly believes that mass products from assembly lines will soon be replaced by mass-produced, customized products and that production will migrate back from low-wage countries to the traditional industrialized nations.
In addition to these personalized products made possible by 3D printing, the “next industrial revolution” will also involve another point: individualized production. It digitizes the manufacturing process, making it flexible, intelligent and therefore efficient. This second trend has the potential to open up our wildest dreams: of workpieces, for instance, which are placed as if by magic onto autonomous transport systems and communicate their processing needs over a wireless network. However, industry is still stuck in the second dimension in some of its operations, two-dimensionality that can be expressed, for example, in stacks of paper.
Johann Hofmann knows the “paperwork nightmare” experienced by many companies only too well. Twenty-six years ago, the production-systems specialist was almost drowned in paperwork. After graduating in mechanical engineering he became a machine programmer at a Regensburg company called Maschinenfabrik Reinhausen (MR), a world leader in tap changers. These are devices used by utility companies to ensure that the voltage in their electricity transmission systems remains constant. As a passionate programmer, Hofmann had been looking forward to doing nothing else all day but feed his computer with numerical codes. But his colleagues from the production department had other ideas: he could hardly ever concentrate on programming because they were constantly interrupting him.
What used to be the day-to-day factory routine in the 1980s is unimaginable for Johann Hofmann today. All incoming orders were exclusively dealt with on paper, put into so-called “workman folders” and then passed around from one department to another. “There were two ladies who did nothing else all day but hand out the folders to the machine operators, tool setters and foremen.” If something in the production order changed – which happened quite often – the workman folder with the handwritten changes went back to the ladies, who in turn passed them on to Hofmann. Although a patient soul, the man from the Upper Palatinate found these constant interruptions hard to bear. And he was only just starting out on his career. He knew something had to change if he was to maintain his passion for his job.
He has now reached his objective, although it has taken him several decades to get there. Today, production is entirely Web-based at Maschinenfabrik Reinhausen. And that means that programming sheets and workman folders are a thing of the past – the production process is now paperless. And that’s by no means the only thing that Johann Hofmann has changed: all the human and non-human actors involved in the production process – that means not only the warehousemen and foremen, but also the tool stores, quality assurance and production machines – communicate digitally with each other and keep each other informed about the current status. This all works with the help of a digital data hub, a so-called cyber-physical system.
Hofmann compares his solution with the organization at an airport. “Imagine a pilot landing his plane and having to do everything himself: he has to find out where he can park, ask the ground marshaller to manoeuvre him to the parking place, and give the ground crew instructions for unloading the luggage. Imagine he has to fill out a form for all that.” That’s approximately what the processes used to be like at MR. Hofmann adds indignantly: “And the day-to-day work routine still hasn’t changed much in many German factories.” Of course, it is possible to work successfully like this, as is clearly demonstrated by German industry’s export strength. But demands on manufacturing companies are rising. Nicolas Maier-Scheubeck, MR’s managing director and Johann Hofmann’s boss, puts the problem in a nutshell: “Every customer gets the specific article they want, however individual, but within the factory the production process must run in a standardized way.”
It took 20 years before this finally worked smoothly. Johann Hofmann has got used to being asked why he needed so long to find a solution: “We first had to get an overview of the data and knowledge involved; then we had to find a way of intelligently linking it all together. That takes a little time when you have such vast amounts of data.” He’s proud that his solution today essentially meets all the requirements of a digital factory. He chuckles and says: “I’m glad it’s now also been given a name: Industry 4.0.”
He walks through the production hall with eyes gleaming and says that he enjoys nothing more these days than listening to the machines talking – and knowing exactly what they are saying. Even decades after joining this family-run business, he still can’t do his programming in peace. But then that’s no longer his job. Although it still happens that colleagues come bursting into his office with a suggestion for improvement, today he’s happy when it happens – because in most cases it means he can further improve the solution and move another step closer to his dream of total networking. ▪