The next step
We interview Axel Stepken, CEO of TÜV Süd, on Industry 4.0 and the opportunities it presents for Germany and Asia.
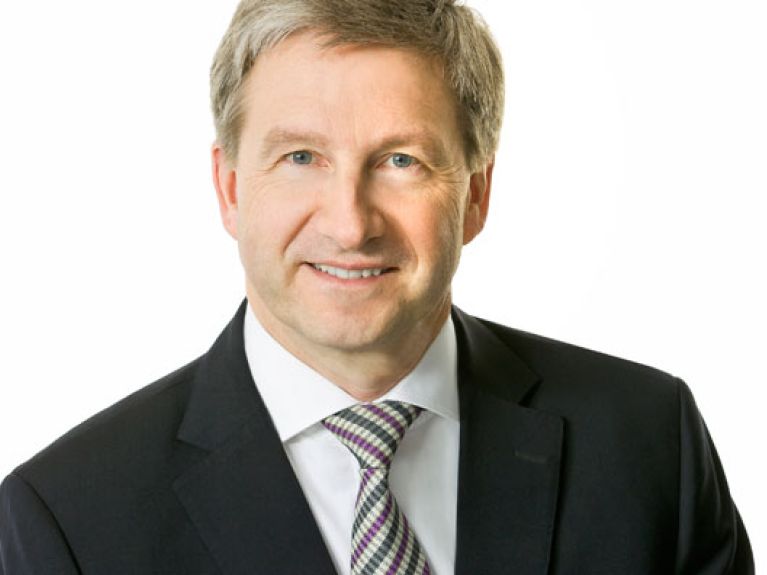
Mr. Stepken, before you became CEO of TÜV SÜD , a leading technical testing company for international industry, you were the Member of the Board of Management responsible for the strategic business segments People and Industry. Industry 4.0 must therefore be very much your subject. What is your appraisal of this development in Germany?
Industry 4.0 and Integrated Industry are terms people use when discussing the comprehensive networking of industrial production. The aim is to give products and machines an “electronic memory”, enabling them to communicate with each other automatically. On one hand, the product tells the machine how it should be processed; on the other, the machine stores data on the product’s requirements and usage, for example, the raw materials and supplies needed or the timing of the next routine maintenance or test. Such data is also useful when modern maintenance strategies are developed or implemented. It will probably take several years before production here in Germany is fully networked, although some companies are already partially producing goods within networked systems. We are unlikely to see completely self-controlling production plants in the very near future.
You are responsible for the ASEAN countries at the Asia-Pacific Committee of German Business. How important are the ASEAN countries for the German economy?
This economic region will develop very positively in the medium to long term, despite the recent currency fluctuations and corrected growth forecasts for some of the ten ASEAN countries. The European Union has recognized the importance of countries like Singapore, Thailand, Malaysia and Indonesia. The conclusion of the free-trade agreement with Singapore in September 2013 will strengthen trade and investment in the country with the highest per-capita gross domestic product in the region. Its population of five million generated a trade volume of 52 billion euros with the European Union last year. This is over one third of the EU’s total trade with the ASEAN countries. But the issue here is not only one of export markets for German and European industry. Major corporations and a growing number of small and medium-sized enterprises (SMEs) are practising global sourcing – in other words, international procurement management – in order to tap cheaper sources of supply. As a result, plant engineering and construction is increasingly shifting to Asian countries while international supply chains are simultaneously becoming more integrated.
In what ways might Industry 4.0 boost economic relations between Germany and the ASEAN countries? What kinds of applications are conceivable?
The increased networking involved in intelligent production would inevitably bring suppliers, customers and service providers closer together. This is also true when they are located in different countries or regions of the world. For example, mechanical engineering companies could find out how customers use their machines in practice after they have been exported. This knowledge would enable them to improve control algorithms and implement updates that, for example, reduce waste, therefore cutting the cost of materials. On the other hand, an intelligently manufactured product could also transmit certain data while it is being used by end customers, thus initiating additional Web-based services or developments that are better tailored to needs. In this context, information and communication technology is a key driver – also in the context of economic relations. Of course, overall legal frameworks must also be harmonized, with attention increasingly focusing on patent and data-protection issues. Industry 4.0 can only develop on the basis of inter-company collaborations that are not hindered by national frontiers. This means that, in the future, companies from Germany and the ASEAN countries will benefit even more from each other – for example, in IT modernization and the standardization of automated communication.
In the near future, according to a recent study by HSBC, the biggest increase in demand for German engineering and technology solutions will come from Indonesia. You have worked in the country for a long time. How do you assess the bilateral development potential?
Thanks to its abundance of natural resources and functioning democracy, Indonesia offers a promising environment for investment and growth. In addition, the vertical range of manufacture in Indonesia is still relatively small at present. Many raw materials are exported unprocessed, so there is great potential, above all in the development of manufacturing – and here especially in the construction of metallurgical and petrochemical plant and equipment. At present the Indonesian engineering sector only has some 400 medium- to large-scale operations and has to import a large proportion of its needs. Moreover, in the future the country will be an interesting target market for high-quality consumer goods from Germany, because a growing middle class with money to spend is emerging as a result of economic growth and the continuing trend towards urbanization. The island nation is already one of the world’s twenty biggest economies.
Your organization, TÜV, primarily looks for optimization potential in production processes. What will be the biggest technological challenges on the road to Industry 4.0?
The technological challenges on the road to Industry 4.0 will doubtless be related to the growing spread of networked systems. This can cause both security risks and safety risks, and these must be brought under control. Not only must a system be made secure against unauthorized access, the focus must also be on operational and occupational safety for people and the environment. Data security in the context of industrial espionage is certainly an important aspect; another issue is protection against sabotage. As regards the implementation of intelligent manufacturing processes, standardizing communication is a particular challenge. Industry 4.0 will only become a reality if there is a common language. To achieve this, all components and systems must interact intelligently – in other words, in ways that are appropriate to each situation, independently of the vendor and in real time. In many cases the communication standards that this requires already exist – it’s just that they need to be observed more strictly and used in a better way. Tried and tested standards also exist for security solutions that make it possible to reliably protect infrastructures, systems and components.
Interviewer: Martin Orth