Modular production
Audi is first German automotive manufacturer to launch a smart factory.
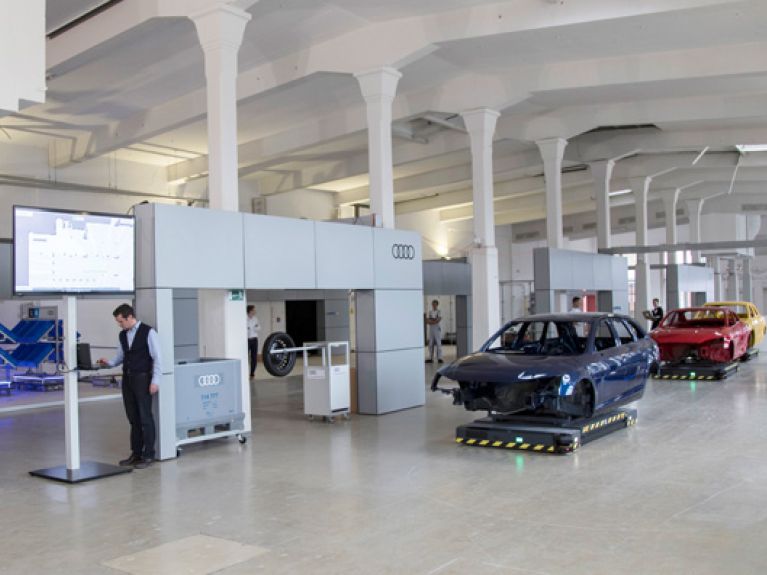
The future is becoming a reality at Audi: the company is the first German automotive manufacturer to switch to a smart factory approach, replacing the conveyor belt with an ultra-modern modular form of production. “Assembly line production only made sense a century ago when just one and always the same product was being manufactured”, explains Hubert Waltl, board member for production and logistics at Audi. “Today our customers want exactly the opposite: every car should be as unique as a bespoke suit.” The idea is to achieve this through modular production.
20 percent higher productivity
Small individual work stations make work processes highly flexible – in terms both of time and place – in the modular assembly approach. The coachwork and components needed for production are transported between the different stations by automated guided vehicles (AGVs). One central computer controls the AGVs with pinpoint precision. It recognises what is needed at each individual station and can therefore ensure completely smooth and uninterrupted workflows. Audi is confident that the modular assembly system will achieve at least 20 percent higher productivity. One simple example: fitting door seals to a limousine takes twice as long as it does to fit them to a two-door coupé. This holds up the production process on an assembly line, whereas work would continue at another station in the modular assembly approach. The system is soon set to go into operation for the first time in the engine production department in Györ in Hungary.