New method for lithium production
Scientists at the Freiberg University of Mining and Technology have developed a way to extract highly sought-after lithium from waste batteries.
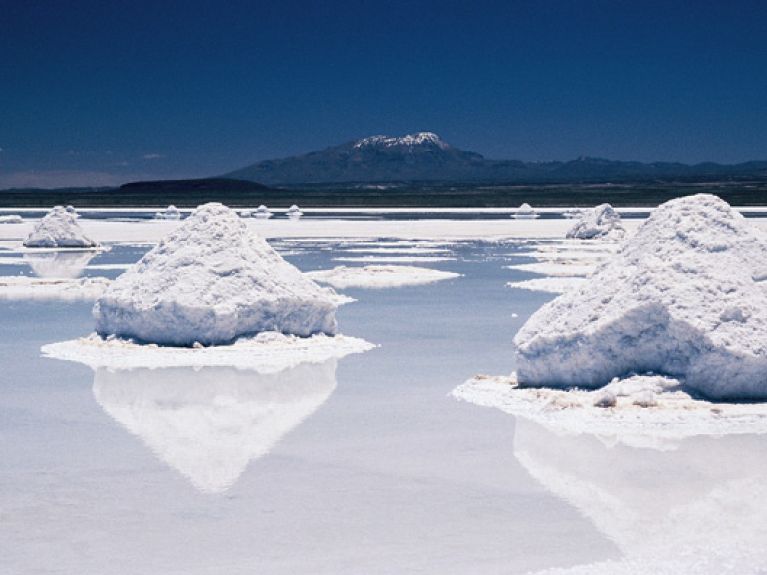
Is lithium comparable to oil as a resource? Few other metals are currently in such high demand as this raw material used in batteries. The light-weight metal can be found in all lithium-ion batteries which are used to power mobile phones, laptops, cameras and increasingly in electricity-driven cars. As a result the prices are increasing at an amazing pace – from less than 6,000 US dollars in 2014 to more than 10,000 US dollars per tonne in the second quarter of 2016. According to a study carried out by the German raw materials agency DERA, demand could actually increase by a multiple of 200 by the year 2035 (compared with 2013).
More economical recycling
It is within this context that a current advance by scientists at the Freiberg University of Mining and Technology gains in significance. They are extracting lithium from waste batteries at costs that lie below the present world market price. The process represents an advanced step in the “hybrid lithium extraction” method already developed in Freiberg. At the start of the process the discharged battery is first crushed. The metals and plastics are then separated from the layering and electrolyte materials, the so-called black mass. This remaining fraction contains not only cobalt but also carbon and lithium. At the moment it is only possible to recover the cobalt from the black mass, while the lithium is lost. The scientists in Freiberg are now adding carbon dioxide and water to act as a filter in the extraction process before the cobalt is smelted out. In this way the lithium contained in the black mass is selectively separated out and transformed into lithium carbonate which can then be used to produce new lithium batteries. The process has now been patented.