Planning for the mobility of the future
An interview with architect and sustainable building pioneer Professor Dr. Werner Sobek about the future of housing and mobility.
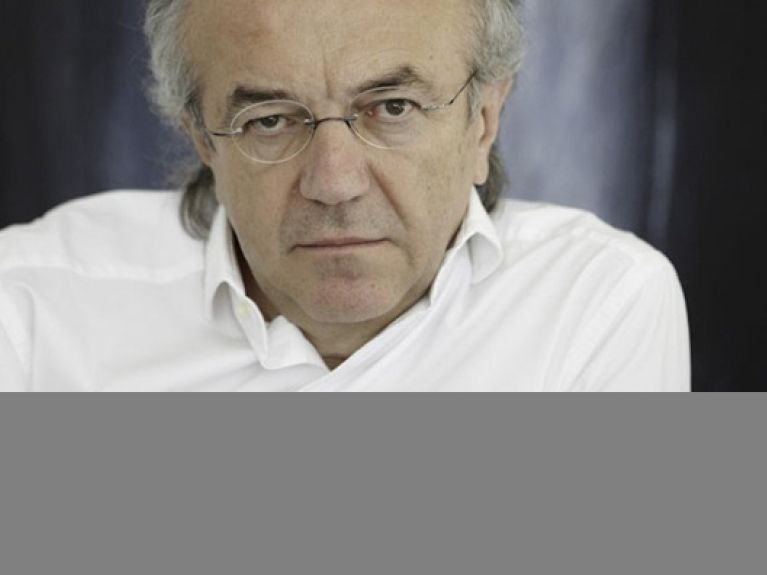
Professor Sobek, what makes your one-family house in Berlin a model for the future of housing and mobility?
This plus-energy house will enable a four-person household to live with all the amenities that you would expect today from a modern building. That includes thermal comfort and visual appeal as well as the house’s individual controllability and adaptability. The family will never need to worry about paying high secondary costs, because the house is heated using renewable energy sources. The energy generated is not only sufficient to supply the house with electricity, but also to charge the battery of the electric car that goes with it. The building is completely emission-free, it can be recycled if rebuilt or demolished and also satisfies all the requirements of the new European building directive.
Why do you consider it so important to think about joint solutions in the fields of construction and transport technology?
Architects and engineers often only look within the confines of the buildings they plan. It is important, however, to understand buildings as part of an urban fabric. Mobility is an important element of this urban fabric, which is why architects and engineers must also take appropriate solutions for future mobility into account in their planning. This applies even more in countries with growing populations than it does in Germany. However, this does not only involve thinking about joint construction and transport technology solutions: today’s planners must learn to plan buildings over their entire life cycle, to see their buildings as units that do not only produce costs during the planning and construction phases, but also during their use, rebuilding and demolition.
What synergies do you see between construction and transport technology?
Synergies can arise during planning and production. In many ways, the car industry can serve as a model for the construction industry: things like integrated planning, platform strategies, recycling rates of 85% and consideration of life cycle costs have all become perfectly natural for major car manufacturers, but have so far hardly been applied in the construction industry. The plus-energy house in Berlin is another example of the Triple Zero® houses that I have been planning and building for more than ten years now. These are buildings that consume no more energy than they generate themselves on average over a year (zero energy), that produce no emissions (zero emissions) and can be separated into different materials and recycled in the course of rebuilding or demolition (zero waste). We need lighthouse projects to increase people’s awareness.
Energy efficiency is an important subject. What other aspects should be taken into account in sustainable building?
We must finally overcome our obsession with energy efficiency during the utilization phase. Germany has become a land of “sealers and insulators”. In the process, however, people have lost sight of the overall goal. How much energy is consumed in the production and installation of heat insulation? How much energy do I actually save over a period of 20 or 30 years once the insulation is in place? And what happens to these permanently bonded composite materials when the building is modernized or demolished? Can the materials be neatly separated and then recycled or are we only left with special waste? After all, sustainability entails much more than just energy efficiency while a building is being used.
Interview: Oliver Sefrin