Do it yourself 4.0
Using digital technology, everyone can design and make things. Welcome to Fab Lab, the living room of the Berlin maker movement.
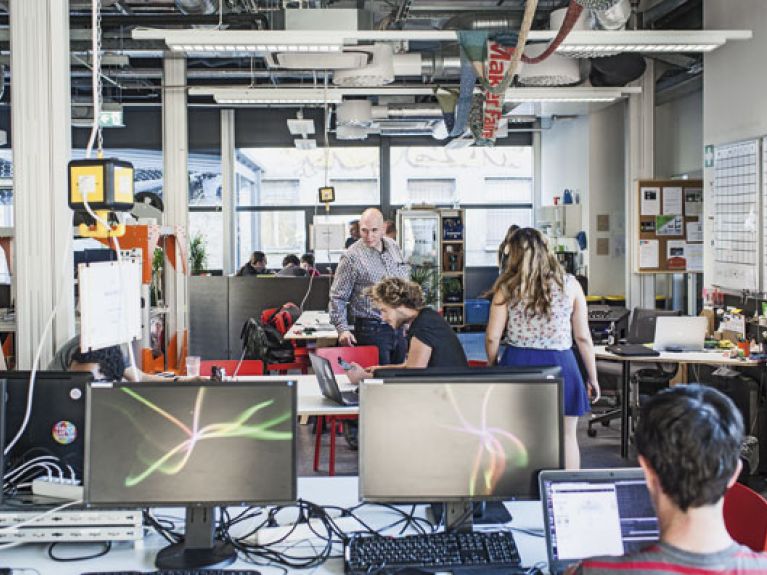
The Bötzow family had achieved practically everything that German industrialists could achieve at the end of the 19th century: they owned the largest private brewery in northern Germany, were purveyors to the court of the King of Prussia and ran a beer garden for thousands of customers. Yet even the most successful firms are often overtaken by events. After less than 65 years the brewery closed down in 1949. Since then the site in the former eastern part of Berlin has been in a kind of hibernation.
If 14-year-old Sami were to look up from his work for a moment, through the window he would have a direct view of the old brewery building with scaffolding and tall weeds. But Sami doesn’t look up. He’s too busy with his project – upgrading his old 3D printer. For the new parts – quite logically – he needs another 3D printer. He has found one here at Fab Lab, a modern inventors’ workshop and fabrication studio.
The low-rise building in the Prenzlauer Berg district is probably significantly larger and better equipped than Bill Gates’s garage ever was. Perhaps, however, the prevailing spirit here is similar: distributed around the open space, groups of young people sit together in front of monitors and electronic equipment. Cables hang from the bare ceilings. Some of them end in power sockets built into multicoloured plastic cubes that swing above the tables. They simply invite you to plug in a laptop and start work.
If you want to work here, though, you have to accept the “Ten Commandants” of the Fab Lab. They are hanging on the wall near the entrance. The first rule is “Be friendly and smile!”, and the second is “Share your knowledge!”. “The people who come here have certain ideals,” says Daniel Heltzel, a manager at the Lab. They include a belief in “open source”, the free publication of programming code, and that inventions should be continuously developed and improved. That sounds harmless, but it contains the germs of major historical changes. The fourth industrial revolution is not only taking place in factories. Industry 4.0 also means that today everyone can design and manufacture products themselves. The people involved, who practically see this as a philosophy of life, call themselves “makers”.
The term stems from US Internet pioneer Chris Anderson. In his 2013 book, Makers: The New Industrial Revolution, he describes the societal and economic significance of digitalisation. “The beauty of the Web is that it democratised both the tools of invention and of production. Any kid with an idea and a laptop can create the seeds of a world-changing company.” In this context, of course, we immediately think of digital companies like Facebook. That’s a limited view, writes Anderson: “Huge as information industries have become, they’re still a sideshow in the world economy.” We can barely imagine, says the author, what the impact would be of a similar development in the real world of things.
This development has long since begun to emerge – for example, at Fab Lab. When Sami tries to tune his 3D printer for top performance, we may see that as the result of a young investigative mind. But it is also the starting point for real economic success stories. Take Soundbrenner, for example. The company sells a wearable metronome. It looks like a wristwatch, but uses vibration to communicate the beat to its user. Musicians who work for stars like Rihanna have tested the device, investors have given 500,000 US dollars to the young founders and they have opened a second office in Hong Kong. Soundbrenner also has a fixed address at Fab Lab, where their success story began. Right next to the laboratory, accessible through a glass door, lies what is known as the coworking space. As soon as projects become more professional, they can rent workspaces here.
At first glance, the coworking space resembles a chaotic open-plan office. But it is much more than that, says Dorota Orlof. The Polish designer and illustrator has now lived in Berlin for three years. She previously worked in many coworking spaces, but never found what she was looking for: creative impetus and space for interaction. Fab Lab offers all of that. “This place has energy.” Orlof is standing with a young man who has just cut an elaborate pattern in a piece of card using a laser cutter. He wants to use it as a template, but isn’t sure which kind of paint to use to fill the fine edges. Orlof gives advice, others join in and talk shop.
In addition to users, Fab Lab team members also help find answers. Regular introductory courses are aimed at new visitors, and every Friday is Open Lab Day. Those who want to come more often can become members. The flat-rate fee for the 3D printer is ten euros a month. At the other end of the price scale, a 150-euro monthly premium membership also provides access to the electronics, textile and wood workshop, to the laser cutter and to the digitally controlled milling machine. A true paradise for makers.
However, the costs cannot be met by the membership contributions alone. That’s why a group of engineers and product designers at the Lab offer consulting services for companies, and the income goes towards the funding. There is also a strategic partnership with Ottobock. The medical technology firm actually owns and lets the premises – the company boss purchased the brewery site and wants to revitalise it.
There is now a lot going on at Fab Lab. Many here see it as a kind of living room for the maker family – they come here to talk, relax and meet people. In the open kitchen stand sofas and a refrigerator with drinks, next to it a box for contributions. Club Mate sells best: the caffeinated soft drink is considered a hip beverage and “hacker pop”. Towards evening the fizzy lemonade is increasingly replaced by beer while music plays in the background.
Morten Modin is still working. The sculptor glances searchingly towards the 3D printer where a transparent jagged object is being created layer by layer. It is part of an artwork that Modin is making for a sculpture park in his Danish homeland. It will take six weeks to print all the parts for the two metre wide and over one metre high work of art. It is made of a material that gradually degrades over time. Modin likes the idea that his first digitally manufactured work will stand in the middle of the natural landscape – and simply disappear after 10 to 15 years. By then, however, the people at Fab Lab will probably be working with completely new technologies. ▪