Industry in transition
From hydrogen technology to high-performance chips: Germany is a leader in mechanical and plant engineering - and is ready for the transformation.
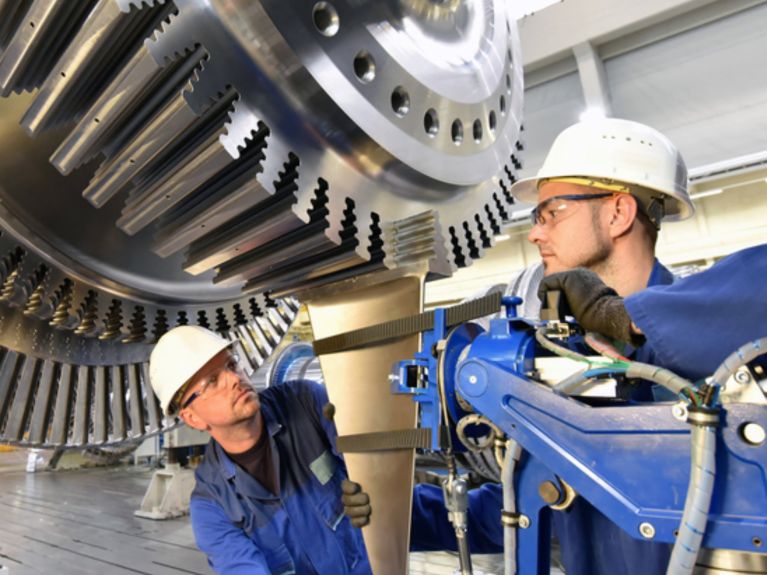
A world without fossil fuels – that was the vision of the start-up Sunfire when it began developing and producing electrolysers in Dresden 15 years ago. This makes the young firm one of the pioneers of the global hydrogen economy: electrolysers use electrical energy to split water molecules in order to obtain the urgently needed hydrogen. With more than 650 employees, Sunfire is now one of the world’s leading manufacturers in this segment and secured around 500 million euros in funding from investors and the European Investment Bank in 2024. “This funding is helping us grow and push forward with industrialising our technologies,” is how Sunfire CEO Nils Aldag describes the firm’s plans.
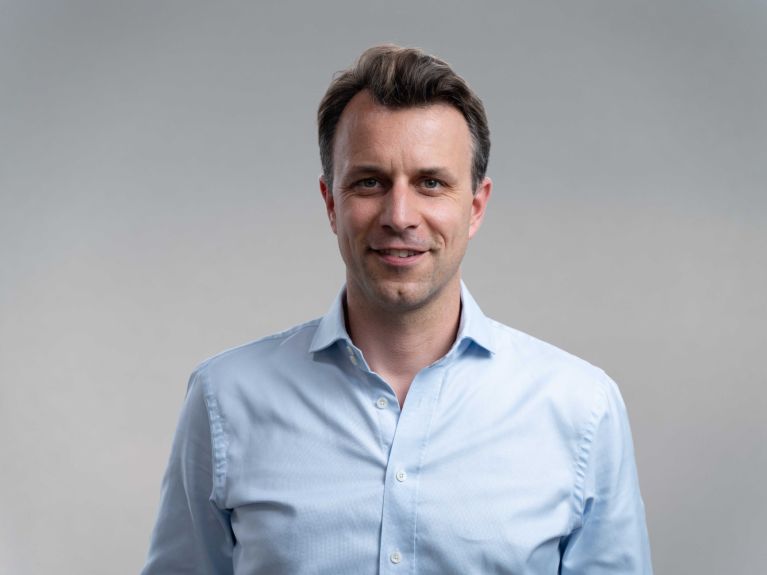
Largest industrial employer
Sunfire is one of over 6,500 German firms in the mechanical and plant engineering sector. Alongside major players such as Siemens, ThyssenKrupp Industrial Solutions, Bosch Rexroth and Trumpf, there are numerous small and medium-sized enterprises (SMEs)and start-ups. Their fields of activity cover everything from drive technology and machine tools to conveyor technology and robotics. In 2023, the industry recorded sales of around 263 billion euros and employed more than a million people in Germany, making it the largest industrial employer. One feature of the sector is its high export rate - more than 80 percent of its products are shipped abroad. According to Thilo Brodtmann, executive director of the Association of German Mechanical and Plant Engineering (VDMA), German firms stand out among their international competitors on account of their “problem-solving expertise, innovation and quality”, among other things. He says that the industry is “the industrial backbone in Germany and, as a technology provider, supplies its products to all other industries”.
AI as a driver of innovation
As is the case in industry in general, digitisation and artificial intelligence (AI) are also changing the way new products are developed and deployed in the field of mechanical engineering. The potential offered by digital twins is huge. “This technology is already being extensively used to create virtual models of physical machines and equipment,” explains Bernd Jung, head of the Industrial Manufacturing practice group at PwC Strategy&. Digital twins allow better monitoring, maintenance and optimisation of machines - and thus increased efficiency and reduced downtime. AI algorithms capture and process large amounts of heterogeneous data from all kinds of different sources to highlight potential for optimisation.

Digital twins of entire factories
One of the pioneers in this area is Siemens AG. In the autumn of 2023, this technology giant from Munich and the mechanical engineering firm DMG Mori, which is headquartered in Bielefeld, already unveiled the first digital twin of the entire machine tool manufacturing process. Shortly afterwards it was announced that digital twins were being developed not only for individual machines but for the energy management of entire factories. This time around, Siemens teamed up with carmaker Mercedes-Benz. “Thanks to the precise modelling of operational and energy usage scenarios, the digital energy twin allows quicker and more transparent decision making in early phases of the planning process,” explained Matthias Rebellius, CEO of Siemens Smart Infrastructure. Arno van der Merwe, vice president of production planning at Mercedes-Benz, added: “The digital energy twin is our solution for successfully visualising, analysing and optimising energy processes in buildings.”
World market leader of chip production equipment
Digital innovations and AI doubtless offer huge potential in mechanical engineering. Nonetheless, they require computing power that can only be achieved by high-performance microchips. And these are produced almost exclusively in Asia and the US. Amid growing international trade conflicts, this dependence could prove problematic and result in shortages for European industry. On the other hand, chip producers worldwide rely on cutting edge technology from Germany. Dutch semiconductor supplier ASML has a quasi monopoly when it comes to the equipment needed to produce high-performancemicrochips and has embarked on an industry partnership with Zeiss and Trumpf – two longstanding German technology companies. While Zeiss contributes ultramodern optical systems, Trumpf supplies the high-performance lasers required by the machines. Thanks to decades of research, billions in investment and a willingness to cooperate closely, the three companies have risen to occupy a leading position in chip manufacture.
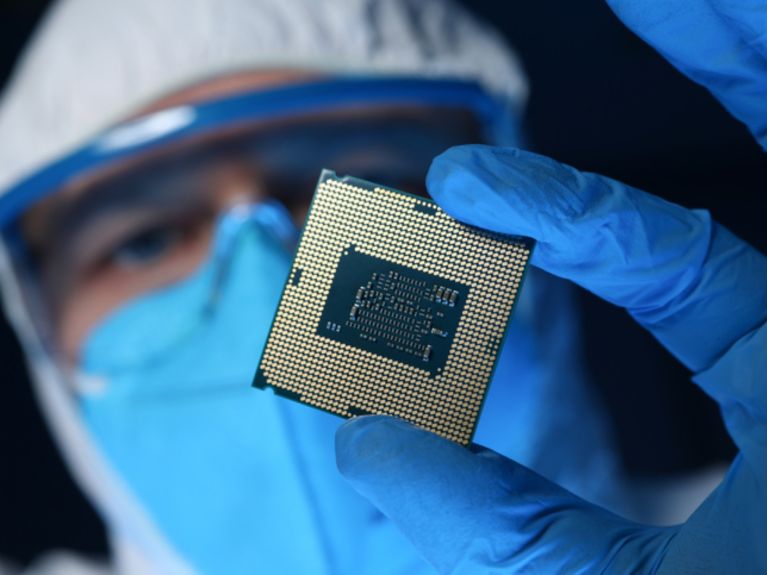
Optimism despite challenges
Like other industries in Germany, the mechanical and plant engineering sector is also facing significant challenges such as economic fluctuations and a skilled labour shortage. It is the high rate of exports that makes the industry particularly susceptible: “Companies are faced with the challenge of responding to profound global shifts, be it in geopolitical terms or the global economy,” says VDMA Executive Director Brodtmann. Nonetheless, the sector is maintaining its high pace of innovation. In 2024 alone, the mechanical engineering industry in Germany spent around 17.8 billion euros on innovation. And around half of the companies surveyed by VDMA in the autumn of 2024 reported that they expected to step up their research and development activities in Germany in 2025. According to the survey, Germany ranked first in a list of the most internationally attractive research locations - thanks in particular to the exceptional strength of the country’s engineering sciences.